A standardized design approach for protective apparel, often seen in industries requiring significant personal safety measures, is frequently employed. This consistent methodology ensures interoperability of components and predictable performance characteristics. For example, a uniform system for integrating padding within garments, specifying placement, material type, and density, contributes to reliable impact protection. Deviation from established guidelines can compromise safety and efficiency.
Adherence to these established design principles offers several key advantages. Consistency in manufacturing leads to reduced costs and improved quality control. Furthermore, the predictable performance of consistently designed protective garments facilitates accurate risk assessment and mitigation. This standardization also simplifies procurement and training, improving overall operational efficiency across various industries. Historical precedents demonstrate the substantial benefits gained through the adoption of such methodologies, promoting improved worker safety and productivity.
Further examination of this standardized approach will explore the specific materials utilized, the testing methodologies employed to validate performance, and the regulatory landscape influencing its implementation across diverse sectors. The discussion will then transition to a detailed analysis of specific case studies illustrating both the successes and challenges encountered in practical applications.
Images References
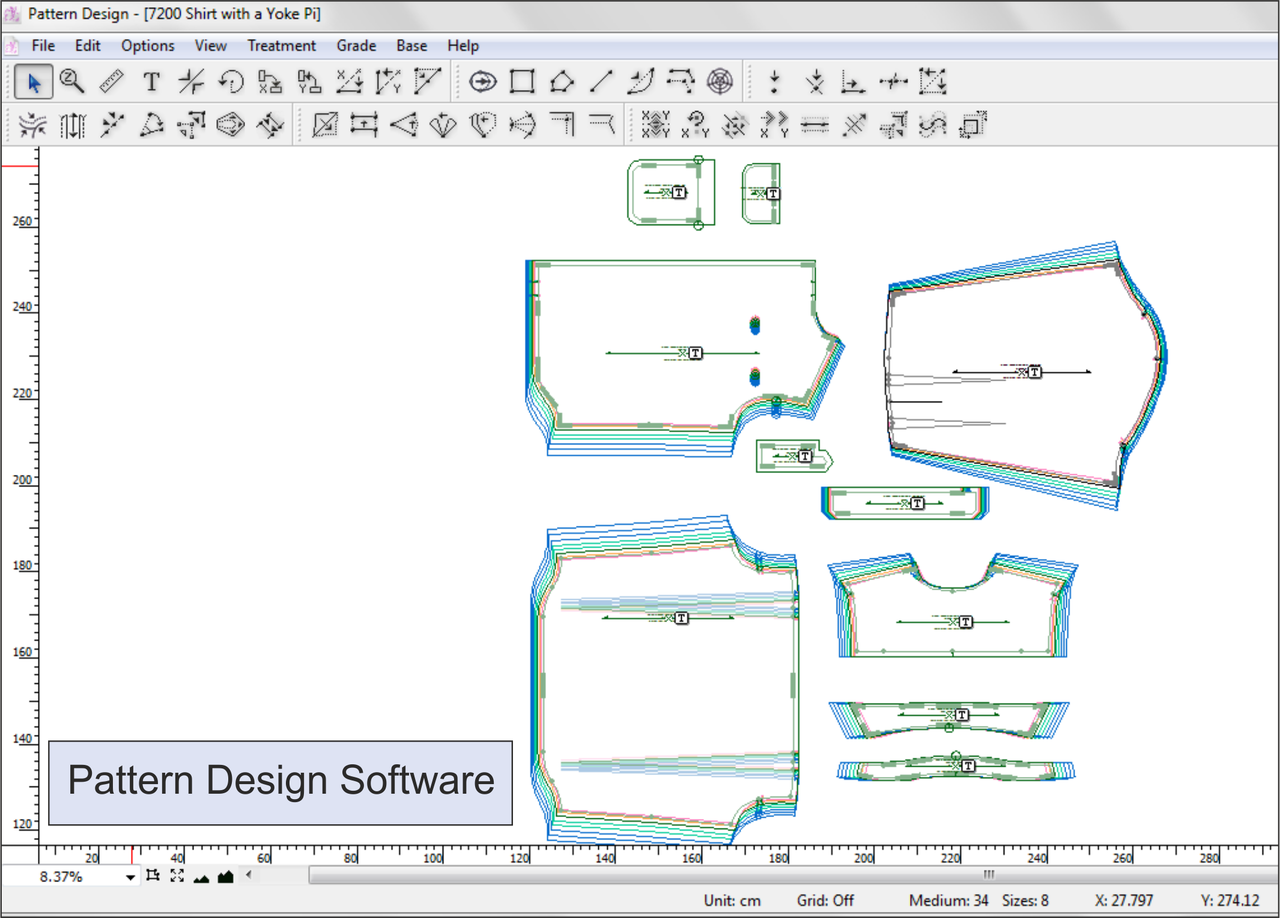
Source: www.cuttinglinesolutions.co.uk
Introduction to PAD Pattern Design cuttinglinesolutions

Source: www.youtube.com
PAD SYSTEM Pattern Design and Marker Making patternmaking 02
Leave a Reply