XG drip irrigation tubing is typically manufactured through a co-extrusion process. This involves melting and combining multiple thermoplastic polymers often polyethylene (PE) and other additives into a layered structure. The inner layer, responsible for water conveyance, may utilize a specific polyethylene formulation for durability and resistance to clogging. The outer layer often incorporates UV stabilizers to protect against degradation from sunlight, and sometimes other additives to enhance strength or flexibility. The tubing is then formed into the desired diameter and undergoes a process that creates the precisely spaced emitter holes or channels for controlled water delivery. These emitters are integral to the tubing’s structure, eliminating the need for separate components. Finally, the tubing undergoes quality control checks before packaging and distribution.
This manufacturing method yields a product with several key advantages. The integral emitter design ensures consistent and precise water application, minimizing water waste and optimizing irrigation efficiency. The use of UV stabilizers extends the lifespan of the tubing, reducing replacement costs and environmental impact. The inherent flexibility of the material allows for easy installation and adaptation to diverse terrains. The development of these efficient and durable drip irrigation systems has significantly contributed to advancements in water conservation in agriculture and landscaping.
Subsequent sections will detail the specific materials used in this manufacturing process, explore variations in emitter design and spacing, and examine quality control measures employed to ensure consistent product performance. The impact of these manufacturing choices on water conservation and environmental sustainability will also be discussed.
Images References

Source: www.rainbird.com
XF Dripline Insert Fittings Rain Bird
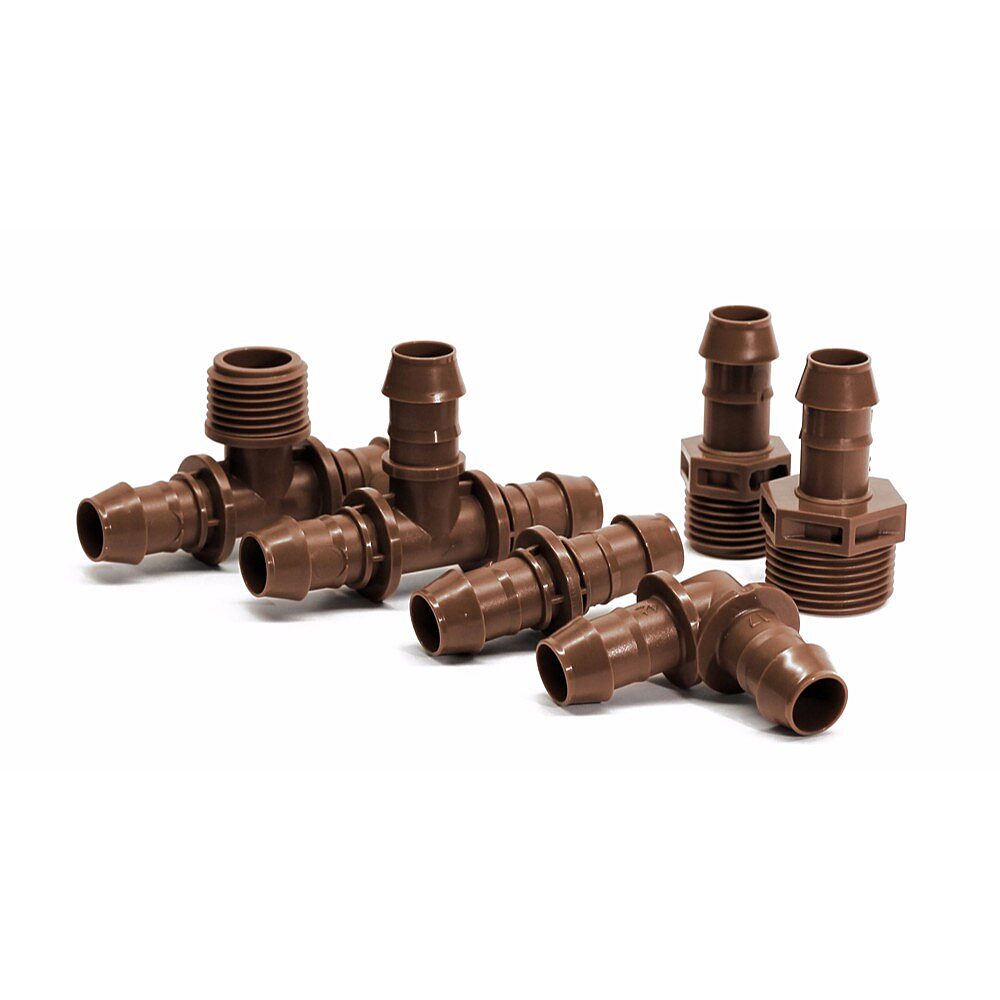
Source: www.shoemakerirrigationsupply.com
Rain Bird XF Series Dripline Fittings Shoemaker Irrigation Supply
Leave a Reply