Xtreme Flow (XF) dripline production involves several key steps. Initially, raw materials such as polyethylene resin are processed through extrusion, creating a continuous tube. This tube is then precisely perforated to create emitter openings, the size and spacing of which determine the water flow rate. Following perforation, the tubing undergoes a series of quality control checks for dimensional accuracy, pressure resistance, and emitter uniformity. Finally, the dripline is often coiled and packaged for distribution. Different manufacturers may employ variations in the extrusion process and emitter design to achieve specific performance characteristics, such as pressure compensation or anti-clogging features.
Precise manufacturing techniques ensure efficient water delivery to plant roots, minimizing water waste and promoting healthy plant growth. This targeted irrigation method conserves water resources significantly compared to traditional overhead sprinkler systems. Furthermore, the consistent flow provided by well-made dripline reduces stress on plants and minimizes the risk of disease spread associated with wet foliage. The development of more durable and efficient dripline materials, coupled with advancements in manufacturing processes, reflects a continuing effort to optimize irrigation practices and enhance agricultural yields.
Further sections will detail the specific materials used in XF dripline production, the intricacies of the extrusion and perforation processes, and the rigorous quality control measures implemented to ensure consistent product quality and reliability. The impact of differing emitter designs on water distribution and plant health will also be examined.
Images References
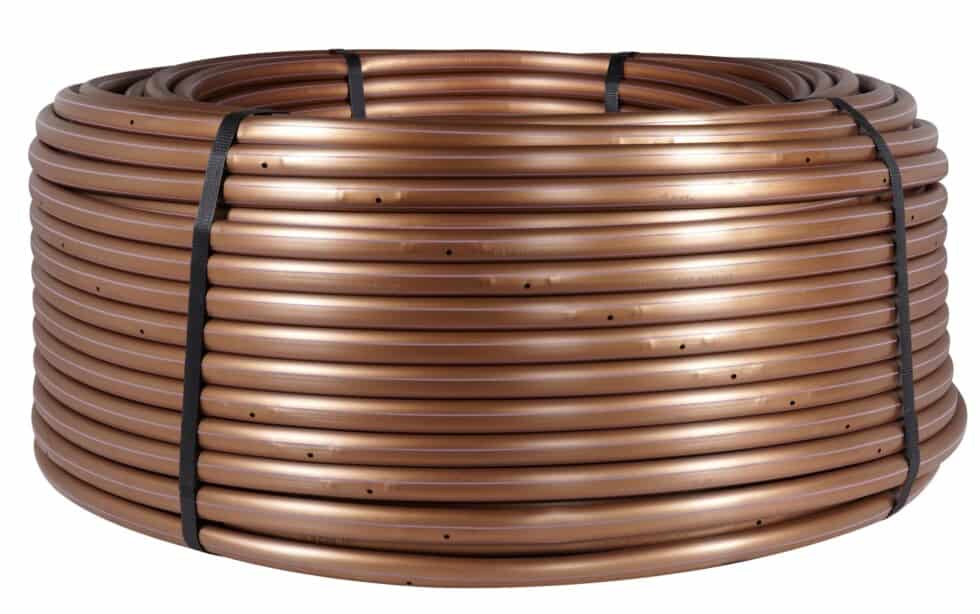
Source: asic.org
RAIN BIRD XFSCV Dripline American Society of Irrigation Consultants
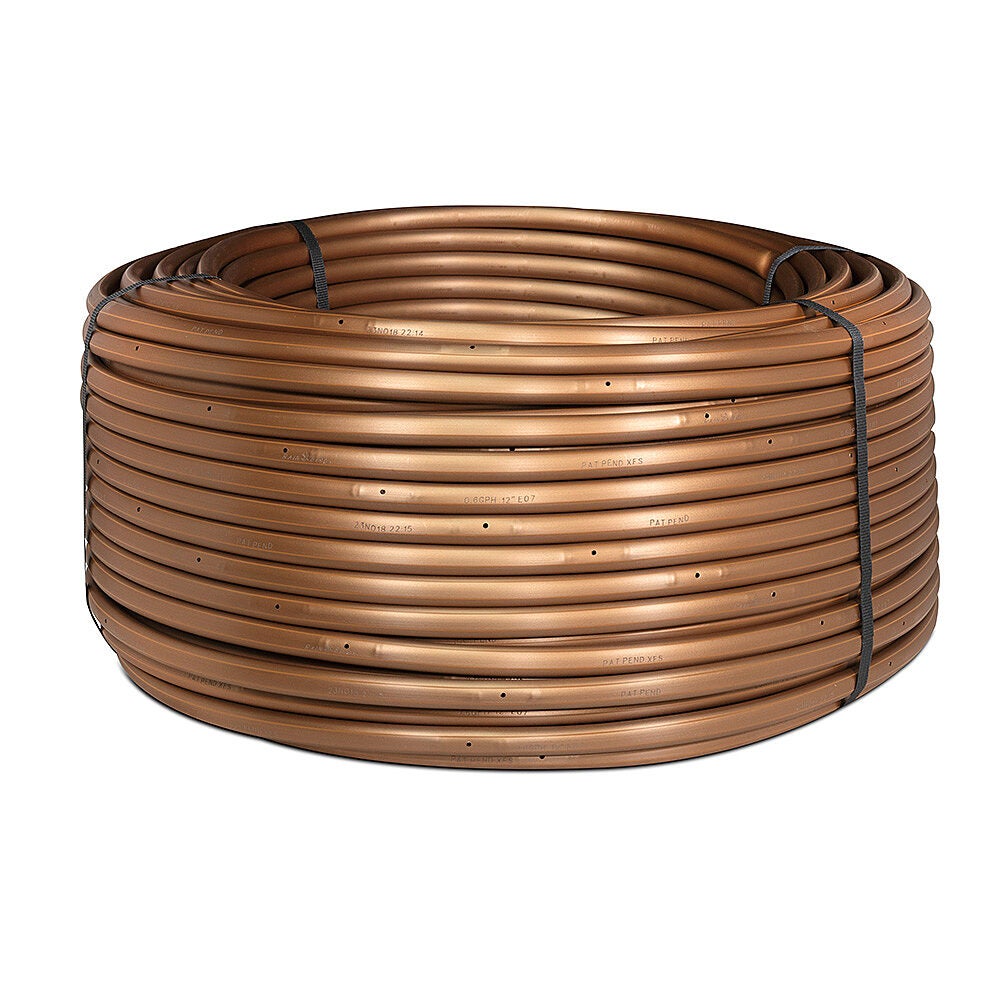
Source: www.rainbird.com
XFS Subsurface Dripline with Copper Shield™ Technology Rain Bird
Leave a Reply