The relative cost of aluminum and steel after anodization is determined by several interacting factors. These include the base metal price fluctuations, the thickness of the anodize layer required, the complexity of the part’s geometry, and the specific anodizing process employed. For instance, thicker anodize layers, often needed for enhanced durability, will increase the overall cost regardless of the substrate material. Similarly, intricate shapes requiring more precise handling during the anodizing process can also lead to higher expenses.
Understanding the cost differential between anodized aluminum and anodized steel is crucial for material selection in various industries. The choice impacts not only the budget but also the final product’s properties such as weight, strength, and corrosion resistance. Historically, aluminum has frequently been preferred for its lighter weight and superior corrosion resistance, potentially offsetting higher anodizing costs in some applications. This cost-benefit analysis has driven innovation in both materials and finishing techniques.
The following sections will delve into a detailed comparison of the cost factors associated with anodizing aluminum and steel, exploring the impact of market forces, production methodologies, and the desired final product specifications. This will provide a comprehensive framework for informed decision-making in material selection for various engineering and manufacturing applications.
Images References

Source: www.sunrise-metal.com
Anodizing Aluminum Metal Surface Finishing Sunrise Metal
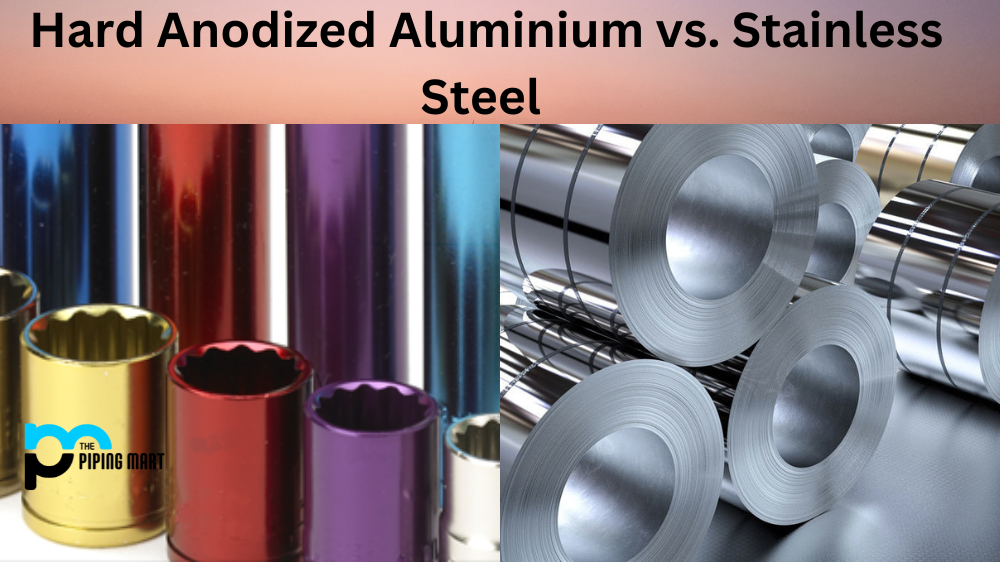
Source: blog.thepipingmart.com
Hard Anodized Aluminum vs. Stainless Steel
Leave a Reply