Aluminum’s inherent properties when cast influence its resulting brittleness. The casting process itself, including cooling rate and alloy composition, significantly impacts the final material’s microstructure and, consequently, its fracture toughness. For instance, rapid cooling can lead to increased brittleness due to the formation of hard, brittle phases within the metal. Conversely, slower cooling allows for the formation of a more ductile microstructure. The presence of impurities also contributes to the likelihood of cracking or fracture under stress.
Understanding the relationship between casting techniques and the resulting material properties is crucial for engineers in various sectors. Careful control over the casting process, alloy selection, and subsequent heat treatments allows for tailoring the final product to specific needs, optimizing strength, ductility, and resistance to fracture. This knowledge has been essential in the development of durable, lightweight aluminum components utilized in numerous applications, from automotive parts to aerospace components. Historically, advancements in foundry techniques have driven significant improvements in the mechanical properties of cast aluminum, enabling its wider use in demanding environments.
Further sections will delve into the specifics of alloy selection, casting methods, and post-processing techniques that contribute to the ultimate mechanical behavior of aluminum castings, including factors affecting impact resistance, tensile strength, and fatigue life.
Images References
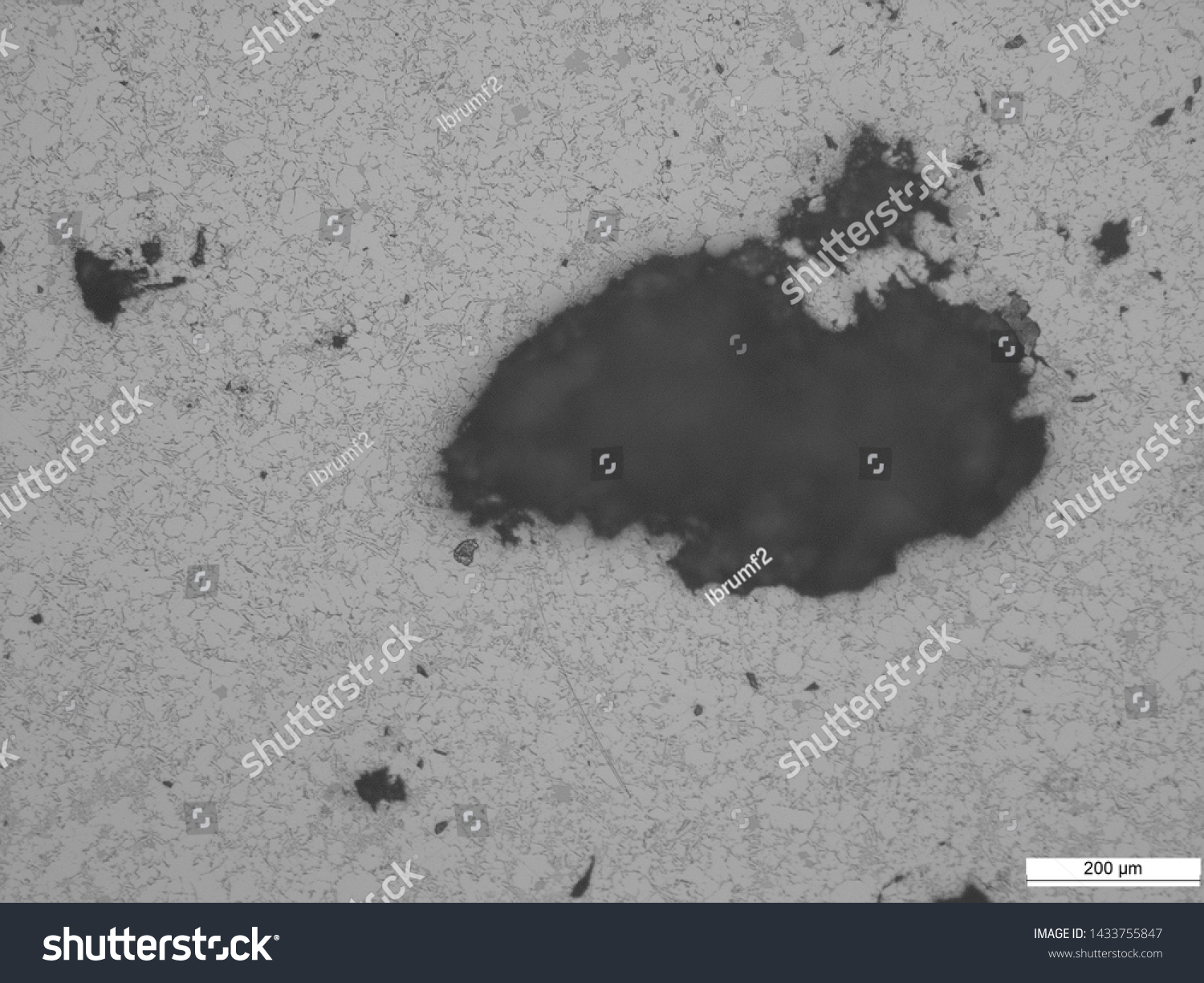
Source: www.shutterstock.com
Brittle Failure A383 Cast Aluminum Handrail Stock Photo (Edit Now
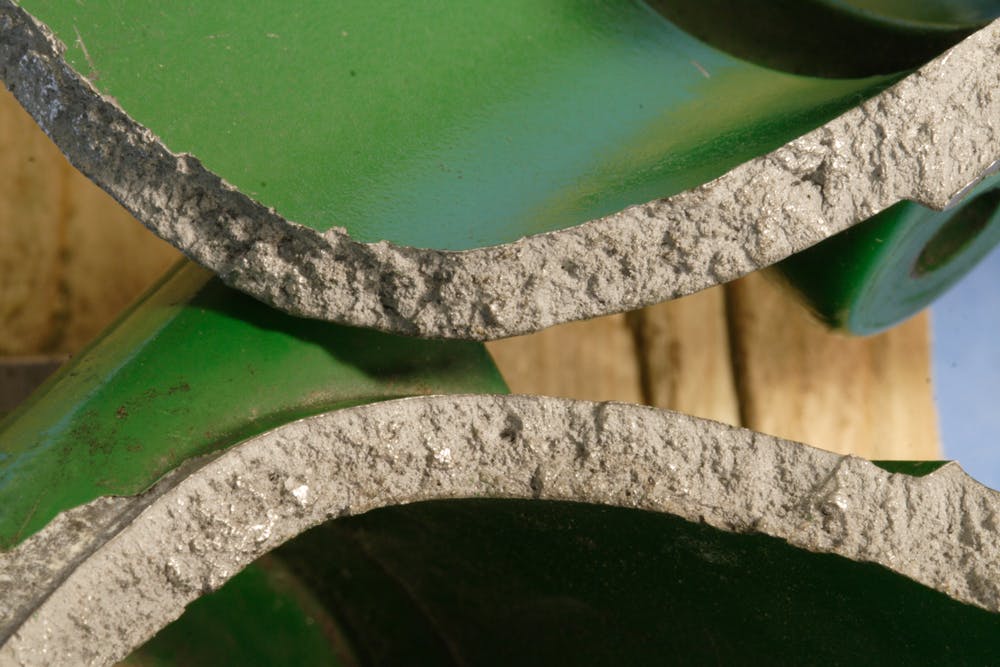
Source: www.xometry.com
Brittle Failure Definition, Causes, and Prevention Xometry
Leave a Reply